This work, published in
The International Journal of Advanced Manufacturing Technology, explores the possibility of applying reverse engineering to spare parts for flexible couplings through additive manufacturing. Although the simplicity of couplings may make them overlooked, they connect elements that transmit power between two shafts, making them an essential component for most machinery used in the industry today. In this study, flexible couplings with different infill densities (60% and 80%) were 3D printed using the fused filament fabrication technique. The original couplings and those manufactured additively were modeled to compare their compression response and energy absorption characteristics, and experimental tests were conducted to validate the finite element analysis. To achieve an optimal material distribution within the coupling structure, a generative design approach was applied using nTopology software. With this innovative simulation-based design, it is possible to reduce the weight of the redesigned part by up to 15.8% by defining the thickness of the internal structure’s wall based on the results of finite element simulation, while maintaining its functionality. Additionally, an economic-environmental study was conducted. The results ensure that the 3D printed prototypes are suitable for replacing the original under its current operating conditions. Additionally, the economic study shows that the redesigned couplings allow companies to save over 2,700 euros per coupling in relation to payments for CO
2 emissions.
See full scientific production at: 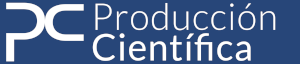